KLIK
Product Design - Toy Design - Sustainable Design
Limited Resources with Endless Possibilities: Building Blocks from Off-cuts
Klik is an intuitive building device and toy design with endless possibilities. Using as many pieces as necessary from 3 simple shapes, each piece friction fits together, they "klik", to create infinite structures and designs. Klik can also be made from a variety of materials, sizes, and colours to become as personalized and unique as the structures you'll build with them.

The PROBLEM
While the design brief was fairly simple, create a container with laser cut components, I had my own problem that makes this project so important to me. I, like many students, struggle with finances as a result of post-secondary costs. I thought I had financially prepared for the year, but I didn't realize how much material costs would add up. This was my final assignment of my first year of university and I had $2.83 in my bank account to work with.
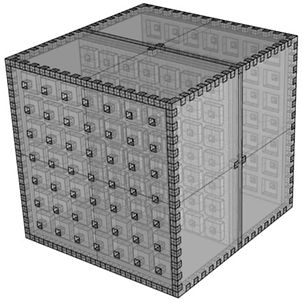_edited.jpg)
The crazy, friction-fit, cubic foot monstrosity I originally modeled for the project... had I not been broke. It was going to hold my writing utensils in each square hole!
THE SOLUTION
OCAD U's shops and studios are amazing in that they have huge scrap bins that are free for students to take from. Acrylic appeared to hold up the best in the scrap bins because it has its own protective covers on them. My design used interlocking, friction fit pieces because I could use scrap materials and no glue, minimizing my costs to almost nothing.
Acrylic off-cuts were sturdy, often unscratched from their wrapping and - most importantly - free!

TOOLS AND PROCESSES
I went through a rigorous process of redesigning the final container form (to fulfill the assignment requirements) and altering shape sizes to compliment the off-cuts I could obtain. I also had to design the shapes with accuracy up to a tenth of an inch, including the "kerf" (the material taken off by the laser), to ensure the pieces would friction fit perfectly. I used Rhino 5 to model the pieces put together and Adobe Illustrator to make the laser cutting file.
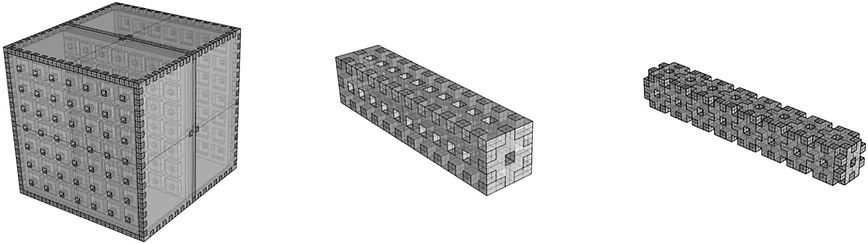_edited.jpg)
THE TEAM
While this was an independent design project, I have to thank Darryl and Phil in the Rapid Prototyping shop at OCAD. They knew how little money I had and that I didn't want to ask my teacher about assistance, so they made sure the only attempt I could afford to laser cut was the only one I'd need. I also have to thank the other shop techs in Plastics and Metal for alerting me every time they saw a great off-cut tossed in the scrap bins.
PRODUCT GALLERY